Operating temperatures of O-Rings
High and low temperatures greatly influence the behavior of elastomers
High-Temperature effects on O-Rings
At high temperatures, the compounds are subject to deterioration causing different effects:
- the hardness decreases, but the effect is reversed if the temperature drops again.
- the percentage elongation increases and, consequently, the load required to break it decreases.
If the high temperatures persist for a long time, they can trigger premature ageing of the compound causing changes in hardness, breaking load, elongation and volume that can reduce the characteristics of the product.
In the presence of high pressure, the decrease in hardness can cause the extrusion effect in one seat. Basically, the O-Ring, made softer by the temperature, is pressed against the wall of the seat where it is housed and, as a result of the pressure thrust, tends to slip into the empty space between the two components on which the seal is made. This effect commonly referred to as “extrusion”, is destructive to the O-Ring and can cause seal malfunctions (see figure in point 1.1).
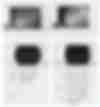
Figure1.1 “The O-ring as an active element”.
See source, click here
Each elastomer has a different coefficient of thermal expansion and is divided into:
- linear: represents the ratio between the change in length at 1°C (or °F) and the original length at 0°C (or °F).
- volumetric: represents the ratio between the change in volume and the product of the original volume and the change in hardness. It is usually equal to 3 times the coefficient of linear thermal expansion.
Elastomers have a much higher coefficient of thermal expansion than metals (about 8/10 times).
This considerable variation should be taken into account when designing an O-Ring seat because the excessive expansion of the compound could cause the seat to fill and cause misalignment of the parts and/or seal problems.
Low-Temperature effects on O-Rings
Unlike the effects caused by high temperature, low temperature usually does not cause permanent changes in elastomers. The most evident effect of the low temperature is the increase in hardness until the product is completely stiffened, but if the temperature increases, the elastomer reacts by returning to its initial state. Defining a limit for use at low temperatures is very difficult. In this regard, there are conflicting theories because many manufacturers of rubber-moulded articles tend to “broaden” the limits imposed by the results obtained in the laboratory with standard tests.
Therefore, there are technical data sheets with limits of use much lower than the tested values, perhaps differentiating limits for static and dynamic seals. Usually for static seals -5°C / – 10°C are “added” to the TR10 reference test value, but these are subjective suggestions based on the experience of use or the fact that “the rubber part does not reach the low temperatures indicated in the specification because it is inserted in a larger system“, etc.
The crystallisation temperature of O-Rings
If an O-Ring inserted in a seat to perform a static seal reaches the crystallisation temperature, the rigidity of the material no longer allows an elastic reaction and, since the article is completely rigid, the sealing effect is lost. Differences in pressure inside the seat can cause the movement of the ring which, being crystallised and rigid, cannot react causing a leakage.
Oringone, for any information please contact us or take a look at our Online Shop