Which materials can an O-Ring be made from? The elastomer families
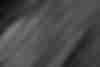
O-Rings can be found everywhere, from small household appliances and systems to the most complex technological mechanics. It is a simple article in its shape and possibilities of use, which is why it remains the best seal for many applications. So what is the difference between an O-Ring used to seal the door of an autoclave and that of an underwater chamber? Or between the ring mounted in a cooling circuit and one in which aggressive gases flow?
In the first place, this is clearly the material with which they are produced.
And speaking of elastomers (we talk about them in general here), these are (almost) all those that can be used to produce O-Rings (and not only): their characteristics, their properties of resistance to fluids and different temperatures, determine the choice according to the different sealing problems to be solved.
The elastomer families
VMQ – Silicone
A compound that guarantees good constant flexibility throughout the temperature range at which it can be used. Excellent resistance to atmospheric agents (ozone, UV rays), good resistance to vegetable oils and fats and brake fluid. Poor impermeability to gases and abrasion. Incompatible with mineral oils and greases. A compound with excellent flexibility at low temperatures (some types can be used down to -90°C), which can be used for electrical insulation and with a low level of combustible elements. Even when exposed to flame, the silicone compound is reduced to non-conductive silicon ash. Good resistance to bacteria, fungi and energy radiation (up to about 100 Rads. Low tensile strength and poor resistance to acids, alkalis and steam above 120°C.
It can be used at temperatures between -60°C and +200°C (with peaks, for special compounds, up to 270°C).
FVMQ – Fluorsilicone
A compound which, thanks to the presence of fluorine, allows good resistance to mineral oils, aromatic and aliphatic hydrocarbons and acids. Excellent resistance to atmospheric agents (ozone, UV rays) and water. Excellent for dielectric applications. Incompatible with silicone oils and steam. Poor impermeability to gases. It can be used at temperatures between -50°C and +180°c, for short periods up to +200°C.
EPDM – Ethylene Propylene Diene
A compound with excellent resistance to ageing, atmospheric agents (ozone, UV rays) and water. Incompatible with mineral and synthetic oils and greases. Good compatibility with chemicals and electrical insulation. It can be used at temperatures between -40°C and +130°C.
Peroxide cross-linked EPDM compound can be used at temperatures up to +150°C and guarantee excellent resistance in hot water, steam (even up to 200°C in the absence of air), ketones, engine coolant.
ACM – Polyacrylate
A compound with excellent resistance to mineral oils and atmospheric agents (ozone, UV rays).Excellent impermeability to gases, ozone and industrial oils.
A compound that can be used at temperatures between -25°C and +150°C, for short periods up to +180°C.
Our company does NOT produce O-Rings with this compound.
FKM – Fluoroelastomer
A compound with excellent resistance to high temperatures and chemical attack. Excellent compatibility with mineral and synthetic hydraulic fluids and vegetable oils. Poor resistance to hot water and steam (although there are specific formulations for these uses that improve performance in this environment. Good resistance to atmospheric agents (ozone, UV rays). Low gas permeability and poor electrical insulation properties. A compound not compatible with polar solvents (MEK), some organic acids, some hydraulic fluids based on esters and methanol, ammonia and some amines. Compatible with high-energy radiation (up to about 100 Rads).
A compound that can be used at temperatures between -20°C and +210°C, for short periods up to +230°C. With specific formulations, the limit of use at low temperatures extends to -45°C (TR10).
FKM materials can be vulcanised with bisphenols (they guarantee better performance at high temperatures) or with peroxides (they guarantee better resistance to vapours and hydrocarbons). The basic polymers used to package the compounds can be:
Copolymers
- Fluoride content:65% / 66%
- Usually defined with the letter “A”
- They are among the most widely used polymers for general applications.
Terpolymers
- Fluoride content:66.5% / 67%
- Usually defined with the letter “B”
- They offer better resistance to fluids and oils than copolymers.
Tetrapolymers
- Fluoride content:67% / 69%
- Usually defined with the letter “G”
- Even better resistance to fluids and oils. Good resistance even to vapour (Viton® GF type), for low-temperature applications (Viton® GLT type) or as a combination of the two (Viton® GFLT type)
TFE/P
A compound with good chemical resistance to acid gases (H2S), alkalis, steam and ozone. Suitable for use with brake and hydraulic fluids. Good resistance to energy radiation. Not suitable for applications involving the use of aromatic and chlorinated hydrocarbons (e.g. acetone), organic acetates and organic refrigerants. It can be used at temperatures between -20°C and +220°C.
FFKM – Perfluoroelastomer
A compound with exceptional resistance to high temperatures, chemical aggression and atmospheric agents (ozone, UV rays). It guarantees chemical resistance similar to PTFE. It is a very expensive compound.
It can be used at temperatures between -20°C and +325°C, for short periods up to +335°C.
AU / EU – Polyurethane
A compound with good resistance to mineral and animal oils and fats and silicone oils and greases. Excellent tensile strength and resistance to abrasion and tearing. Excellent resistance to energy radiation (up to about 100 Rads. Excellent for dynamic applications where a considerable load is required. Poor resistance to hot and humid environments.
It can be used at temperatures between -30°C and +100°C.
Our company does NOT produce O-Rings with this compound.
NBR – Acrylonitrile Butadiene
A compound with excellent resistance to mineral oils and greases. Good impermeability to gases. Good flame resistance. It is not very suitable for resistance to atmospheric agents (UV rays, ozone).
It can be used at temperatures between -30°C and +110°C. With specific formulations, it is possible to extend the limit to low temperatures down to -50°C.
Depending on the acrylonitrile (ACN) content NBR compounds have lower flexibility at low temperatures, higher resistance to permanent compressive stress, gas permeability, better heat ageing characteristics and ozone resistance, higher tensile strength and abrasion resistance, hardness and density. The higher the ACN content, the higher the resistance to aromatic hydrocarbons. The lower the ACN content, the better the flexibility at low temperatures. Generally, the best compromise for most applications is an average ACN content.
The percentages of ACN contained in the compound are considered:
- Low percentage: up to 30% ACN content
- Average percentage: 30% to 45% ACN content
- High percentage: > 45% ACN content
HNBR – Hydrogenated Acrylonitrile Butadiene
A compound obtained by hydrogenating the nitrile copolymer (NBR). Excellent abrasion resistance and remarkable mechanical performance while maintaining excellent resistance to atmospheric agents (ozone, UV rays, oxygen), mineral oils and greases, hot water and steam (up to 150°C) and H2S gas. HNBR compounds cross-linked with peroxides have better resistance to permanent compression and heat failure, while those with high nitrile content (ACN) have better resistance to mineral oils.
It can be used at temperatures between -50° and +150°C.
CR – Polychloroprene
A compound with excellent resistance to atmospheric agents (ozone, UV rays), sea water (and salts in general) and abrasion. Excellent gas impermeability and compatibility with Freon® and refrigerants in general. Good resistance to mineral oils and greases.
It can be used at temperatures between -30°C and +100°C, for short periods up to 120°C.
SBR – Styrene Butadiene
A compound with good mechanical characteristics compatible with silicone oils and water. Not compatible with mineral and vegetable oils and poor resistance to atmospheric agents (ozone, UV rays). It can be used for dielectric applications.
It can be used at temperatures between -40°C and +100°C.
Our company does NOT produce O-Rings with this compound.
NR – Natural Rubber
A “natural” compound obtained from the “Hevea” rubber tree (but it is also possible to produce it artificially).Excellent elasticity and resistance to abrasion and wear. Poor resistance to atmospheric agents (ozone, UV rays). It can be used for dielectric applications. Not compatible with mineral and vegetable oils, hydrocarbons and solvents.
It can be used at temperatures between -70°C and +80°C.
Our company does NOT produce O-Rings with this compound.
IIR – Butyl
A compound with excellent gas and air impermeability characteristics. Excellent resistance to atmospheric agents (ozone, UV rays) and excellent insulation properties. Not compatible with mineral oils and greases, hydrocarbons, various lubricants. Good vapour resistance (up to 110°C). The IIR compounds can be polymerised with various halogens (chlorine/bromine) to improve resistance to certain chemical media, but with a deterioration in electrical insulation and moisture resistance. Good resistance to use with vegetable oils.
It can be used at temperatures between -40°C and +130°C.
Our company does NOT produce O-Rings with this compound.
For more information and technical details, please contact us.